关注 iPhone 的读者大概率知道,今年 iPhone 16 系列在外观设计上有着为数不多的一点小变化,这就是进一步缩窄的「四边等宽」屏幕黑边。虽然仅有零点几毫米的缩窄,它带来的却是更大的屏幕视野,和一种更为沉浸的视效,相信上手感受过真机的朋友会有同感,搭配上 R 角的整体性外观设计,令许多用户感到极度舒适。
十一假期前,我带着 iPhone 16 Pro Max 来到青岛,参与 OPPO 在这里组织的一场面向媒体的新机沟通会活动。在这里,我第一次上手体验了 Find X8。这款 OPPO 新一代的旗舰直屏给我的第一感觉是,轻薄精致,屏幕正面的四边等宽极窄边框,给我带来了同样十足的视觉冲击力。在掏出和 iPhone 16 Pro Max 做对比的过程中,我产生了几个疑问:这个四边等宽的窄边框技术,是来自供应链的通用能力吗?如果不是,OPPO 为什么可以几乎同期推出同样的超窄四边等宽产品?
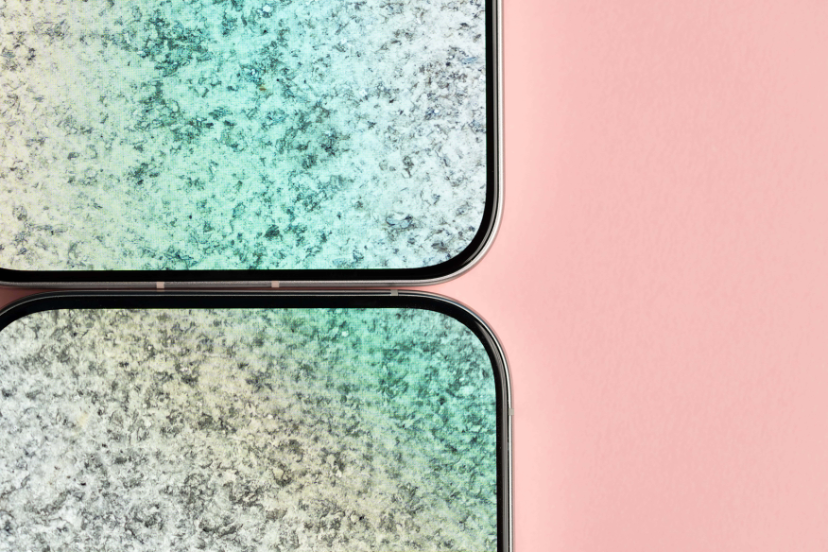
只看边框宽度,你猜谁才是 iPhone?
▍四边等宽极窄边框,花了一个亿?
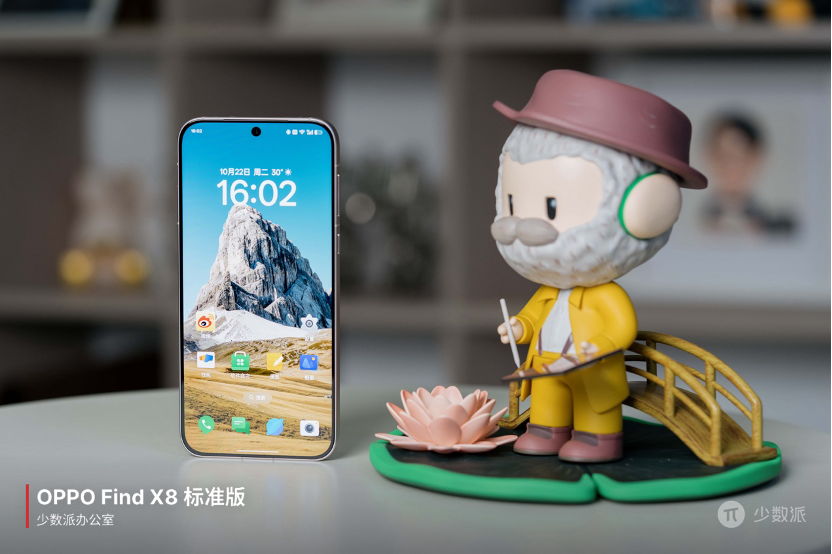
与此同时,我在社交媒体上留意到 Find X 系列产品经理的爆料:为了实现 1.45mm 的四边等宽极窄边框,OPPO花了三年时间,投入超过一个亿资金,专门打造了超过 100 米的现代化封装产线,并提到了背后的「芯片级封装」技术,这些信息激发了我深入了解其背后故事的强烈好奇心。除了技术,我还想探究,这一个亿的投入究竟花在了哪些方面?与用户获得的收益相比,这样的投入是否值得?带着这些疑问和好奇,我们近水楼台先得月,来到了位于东莞的OPPO超窄边框屏幕封装生产线,为大家一探究竟。
在全套严密「武装」之前刚被强风吹扫后,我又再次进入吹尘风箱,准备踏入全手机行业防尘级别最高的产线之一
在分享此次探厂经历之前,我想先简单介绍一下,为什么手机厂商缩窄黑边和「大下巴」如此困难。全面屏一直是科技圈和大众用户的终极理想。在许多科幻电影中,手机甚至成为一块透明的玻璃,完全没有边界的概念。但实际上,技术的进化并非易事。在黑边下方,不仅隐藏着屏幕的精密走线和驱动芯片,还有必要的防撞安全区和公差缝隙。要想缩债屏幕黑边,背后牵扯到层层的技术连锁反应。iPhone 是一个划时代的产品,它定义了大屏智能手机的基本形态。如果技术允许,乔布斯一定会在第一代 iPhone 就直接打造全面屏的手机。遗憾的是,受技术所限,当时的手机屏幕上下两端必须留出放听筒、麦克风、传感器,以及驱动屏幕显示和触控的多个芯片等零部件的空间,这也是导致早期的智能手机,都有着很宽的额头和下巴。在这个时代,屏幕的组装工艺叫 COG(Chip On Glass)。从初代 iPhone 到 iPhone 8,尽管屏幕的尺寸在不断变大,但「大额头+屏幕+宽下巴」的基本结构却没有发生改变。在此期间,以三星为代表的海外安卓品牌,以及国内众多的手机厂商都开始围绕缩减屏幕「额头」和「下巴」的尺寸发力,譬如 OPPO 经典的 R 系列(也就是如今 Reno 系列的前身),就通过持续压缩屏幕头尾两侧的盖板面积,创造更大的屏幕,加速并引领了手机行业在追逐「全面屏」的进程。手机的额头和下巴尺寸一直在持续缩减,行业用十年的时间从初代 iPhone 的宽额头和宽下巴做到了 OPPO R11s 的窄额头、窄下巴在 iPhone X 到来之前,iPhone 的尺寸一直在变大,但「额头」和「下巴」的宽度始终没有实质性的缩减。相较之下,安卓阵营则一直在尝试在窄额头和窄边框方向取得突破。激烈的竞争也促使苹果拿出了更具突破性的全面屏产品随着屏下各种元器件的不断进化、整机结构堆叠的创新突破,以及屏幕挖孔技术的日臻成熟,手机屏幕的边框不断缩窄,额头也逐渐消失,但底部边框的宽度仍无法达到令人满意的程度,其「罪魁祸首」正是屏幕下方的芯片和排线。为了保证屏幕的正常使用,芯片和排线必然存在,而这些走线和元器件始终会占据一定空间。直到 OLED 柔性屏幕的技术成熟,工程师们才创新性地将芯片贴到了屏幕排线上,并将其翻折到屏幕背后,进一步缩窄了黑边。苹果 iPhone X 之后的产品就是依靠这个方案实现了视觉上的四边等宽,而这个工艺就是如今流行的 COP(Chip On PIastic)。COP 通过优化芯片和排线结构的方式大幅减少了空间占用,这也是目前手机「下巴」的主流结构COP 结构第一次广为大众所知,正来自 iPhone X 的这条宣传片,可以清晰看出屏幕下方排线的弯折方式排线反折方案虽然巧妙,但并非完美。由于排线的位置相对脆弱,机身内部必须预留一定的碰撞保护空间,这使得进一步缩窄黑边受到物理空间的限制。在研究如何进一步缩窄「下巴」的过程中,OPPO 的工程师们想到:是否有可能将排线部分从脆弱的受保护区,变成强韧的结构件,进而缩减这片安全区?针对这个问题,答案也随之浮现——将整个排线的反折部分用高分子材料进行液态封装,再进行固化定型,让高分子材料与屏幕融为一体,就可以彻底缩减预留的缓冲空间,进一步缩窄黑边。这就是 Find X8 在发布会上公布的「芯片级封装」工艺。传统点胶工艺下,排线和手机边框之间必须预留足够的安全区,这也是手机行业的经验禁区Find X8 的屏幕通过封装工艺实现了新结构,省出了一大片宝贵空间这个过程看似轻描淡写,被我用几句话就介绍完了,但仅仅为了让屏幕的「大下巴」变得和其它三边同宽,整个行业就花费了近十年的时间,其间涉及无数技术的革新与工艺的迭代。而这一切的背后,更是手机厂商与众多零件厂商合力研发的结果。前面我们讨论了理论知识,接下来通过真实的探厂经历,带大家看看为了去掉多余空间,OPPO 的工程师们具体都做了什么。由于涉及较多制造行业的专业术语,我尝试用做一道好菜的过程进行类比,帮助大家能更好地理解这个封装工艺和关键技术。我们都知道,一道美食的关键就是食材要足够好。既然是做防护封胶,首先要找到最合适的封装胶水。它不仅需要强度高、耐腐蚀,还要能够相对快速地完成固化,以满足大批量的自动化生产需求。OPPO 团队花了六个月时间,对环氧胶、气凝胶、热熔胶、AB 胶等 27 种胶水方案进行验证测试,最终选择了与专业胶水厂商联合定制 UV 胶水。OPPO 定制的 UV 胶水需要低温保存,经过严格的回温处理后才能投入使用,整齐地排列,就像一颗颗小炮弹
不仅要验证胶水的本身的可靠性,还要验证胶水与其它组件的兼容性,包括对屏幕显示和排线的腐蚀和互斥,以及在不同温度下,应力的一致性。作为连接和保护屏幕的关键层,OPPO 工程师需要模拟用户日常使用中的各种意外因素,包括汗液、雨水、空气、清洁剂等不同材料的接触,以及极寒、极热、碰撞等外部环境的变化,确保胶水的稳定和可靠性,仅各个材料之间的兼容测试就接近 3000 次,产生了无数的排列组合。定制 UV 胶遇到可见光的蓝光部分会固化,所以整条产线都必须使用特殊波段的黄光,我的参观之旅也在这种奇特的「温暖」氛围中进行
食材选好了,需要为它配备最佳的最佳盛具来保证出品的风味。如果说胶水的研发和定制是一场大型排列组合的数学游戏,那么模具部分的研发则更像是「针尖上起舞」的精度游戏。为了控制封装胶水的精度,需要先将屏幕组件固定在一套的高精度模具上。除了选用高精度的不锈钢磨具,最关键的是模仁的研发和定制。由于屏幕模组本身非常脆弱,只有使用玻璃面板加硅胶边条来承载封胶过程,才能同时兼顾强度和韧性。为了保证工艺的精度,Find X8 的屏幕封装对模仁的公差要求不超过 0.03 mm,相当于发丝直径的 1/3。要实现如此高的精度,就如同建设一座足球场,但地面高低差只能有一部手机的厚度。因此,为了保证这一精度,每个模仁在产线上每经过数十次使用,就必须更换检查,并进行重新修复。这无形中又增加人力投入和材料成本,但这也几乎是确保如此精度和超高成品良率的唯一有效方式。柜子里整齐地分类摆放着封装流程中的关键零部件——单个价值数万元的模具在探访过程中,OPPO 的工程师们跟我分享了模仁设计中遇到的几个难题。聆听过程中,我产生了深刻的共鸣。此前,少数派仅是制作一个简单的手机壳,都会遇到量产粘接气泡的问题,导致延迟交付。硬件制造需要极其严谨的考量和测试,除了制程设计上的经验,还会有无数意外情况等着你,它们可能来自温度、力度、光线、材料等各个方面。选择自研就没有捷径,只能不断地反复测试,找到问题点,再反复地优化调整。每一款伟大的硬件产品背后,创新的设计只是开始。将设计方案导入制造产线的过程中,会遇到无数令人崩溃的挑战,而这些挑战不像做软件产品,可以上线后调试和修正。你必须做到 99.9% 的可靠性,才能推进下一步,而到了下一步,又会有一堆新问题等着你。搞自研不是一句口号,而是真正的自我「折磨」。OPPO 工程师单是在模仁设计与落地投产这一步,就进行了大量试验,尝试了不少于 20 种方案。参观产线时,看着各种精巧的模具和制程设计,我似乎明白了苹果 CEO 库克在一次访谈中提到的:中国超强的工程化能力和制造业人才是不可替代的。食材和厨具都已就位,我们需要打造一个专属「厨房」,好好地「烹饪」一番。这个「厨房」就是 OPPO 专门设立厂房并引进的国产最先进的低压注塑封装产线。要应用这条产线并不简单,首先需要一个 125 米以上的直线空间,同时还要达到千级无尘的环境。且由于产线设备本身很重,如果放置在高层厂房,就容易造成轻微震动,影响工艺精度。于是,OPPO 单独为这条产线打造了一个全新的车间,每一块 OPPO Find X8 的屏幕都会在这条专属产线中封装,并最终走到用户手中。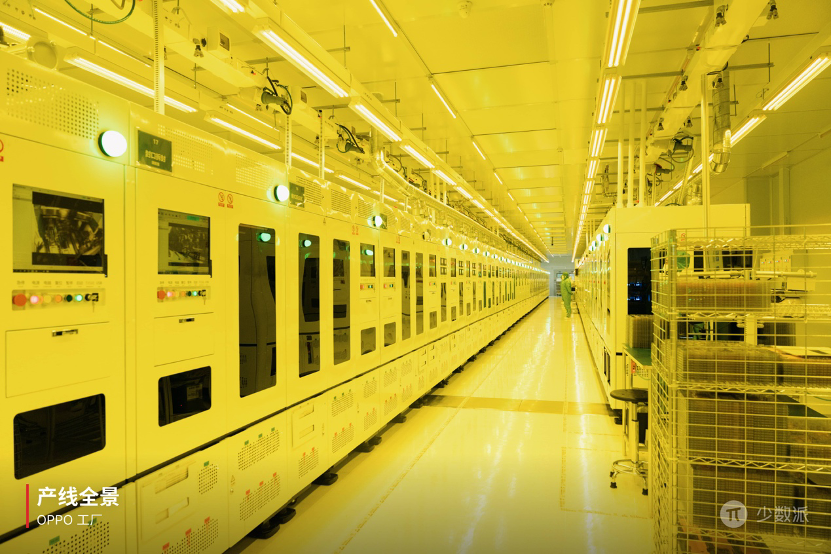
这条总长超百米的千级无尘产线,见证着安卓首批迈入 1.5mm 极窄四等边量产屏幕的诞生
虽然都是「做菜」,但 Find X8 屏幕的这道「菜」却对「食材」的温度、压力乃至「烹饪成熟时间」都有着严格要求。在这条产线上,相较于此前的传统点胶工艺,整体的封装工序不仅大幅增加,工序的难度更是上升到了难以想象的程度。屏幕模组与模仁自动化组合,抽取真空,进入封胶过程。胶水从两个特定的孔道流入模具,以均匀的流速穿越排线空隙,灌满模具,随后进行快速光固化。「菜」做好了,接下来就要「出锅装盘」。屏幕的脱模设备通过引入微米级的超精准风力控制技术,打破真空,再用气压吹开屏幕模组,进行二次固化。整个过程中,不能有任何气泡、溢胶产生,因为哪怕几微米的瑕疵,都可能无限放大用户日常使用中可能出现的故障和风险。已经完成封装的屏幕。正是图中白色半透明的封胶部分,为排线和屏幕边框提供了更强的防护,同时缩减了传统工艺必须额外留出来的安全区在以上各个环节中,可能会出现各种问题,例如两段胶水的流速不一致、脱模力度不稳定、固化灯光温度不均匀等等。因此,无论是具体的每个流程,还是流程之间的协调,都需要通过各种参数标定和试验才能完美同步。经过上千次的反复调试,目前,OPPO 这条新产线已实现每天 上万片的屏幕模组封装量产,良品率更是达到了令人惊叹的 99.9%。做一盘好菜,看菜谱很简单,但要做好却很难。一个工艺的精进,带来的是连锁反应。与之前的边框点胶工艺相比,OPPO 的这套全新封装工艺涉及大量的材料研发测试、自动化产线测试、单体屏可靠性测试、整机结构和堆叠测试等。从产前到产后的各项测试项目,与传统工艺相比,复杂性呈指数级上升。据 OPPO 工程师透露,Find X8屏幕封装项目的单技术验证数量就超过了常规手机整个项目的验证数量。其中,仅屏幕的测试验证投入就高达 6 万片,整机测试投入达到 4000 台。这就像一位大厨,为了做好一道稀世佳肴,所准备的食材和投入的工序必然超过普通厨师做一桌菜的投入。但也只有这样,才能让这款要求发丝级精度的屏幕变得可靠,在追求优秀设计的同时,保护消费者的利益。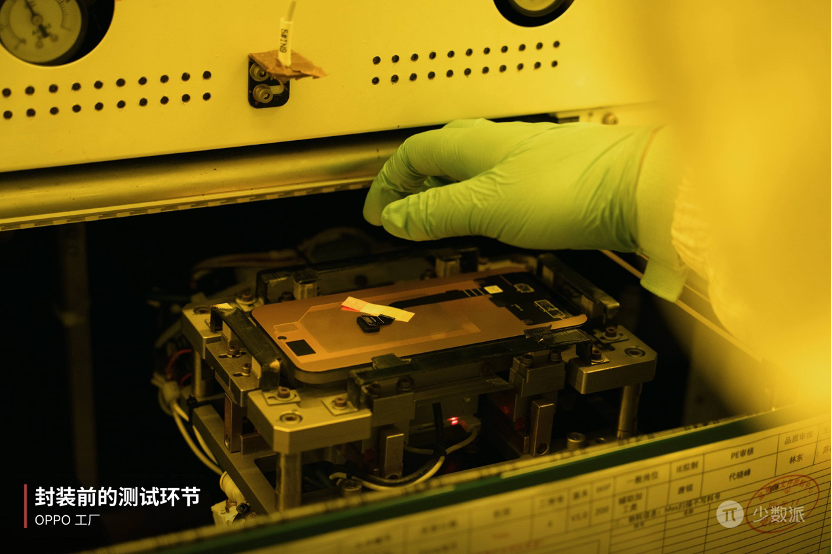
在制作「四等边极窄边框」这道「菜」的过程中,OPPO 不仅做得精细,而且做得智能。为了实现全产线更高的自动化和实时的智能管理,在保证良品率的同时不断优化生产流程,沉淀超高标准全新屏幕封装产线的智能制造宝贵经验,OPPO 投入了 300 多位工程师,为整条产线的自动化管理开发了一整套全新的系统,该系统将所有生产数据进行采集和分析,为产线的智能管理提供更好的数据分析与预测。这套系统也将打通OPPO在重庆、印度、印尼和阿尔及利亚等全球各地的工厂,完成高标准产线在全球制造数智化管理系统中的重要升级。产线上的每部机器、每道流程都有实时的数据统计和录像监控,而所有数据都将通过云端上传至 OPPO 数智化管理中心。管理人员在自己的电脑上就能随时看到全球任何一台设备的生产情况并实施操控
这不是我们第一次参观 OPPO 工厂。几年前,我就曾深入了解过他们的 SMT 贴片产线和总装工厂。在流行外包代工、追求轻资产的时代,OPPO 却一直坚持自建工厂,短期来看,的确费力不讨好,但从长远来看,长期积累的制造人才和工程经验,正是这次 Find X8 屏幕工艺突破的关键基础。这次参观,OPPO 给了我们最大的开放度,允许我们拍摄记录每一个工艺流程细节,同时聚集了研发、结构、整机的多位工程师,给我们科普技术工艺,解答各种问题,分享了很多技术导入的幕后故事。我能充分感受到他们遇到的各种困难时的焦虑,以及攻克技术难关后的喜悦和自豪。在 OPPO 工厂度过的一整天,我仿佛也融入了这个团队,和他们一起面对工艺突破的挑战,一起享受研发成功带来的喜悦,也一起期待消费者拿到极窄四等边的 Find X8 之后的心动瞬间。OPPO 从 2020 年底开始预研 COP 封装工艺,2021 年初确定整体方案,2021 年底在 OPPO 手表上进行试产验证,2022 年中开始手机上的技术预研,直到 2024 年初才确定方案。随后不到一年的时间,就完成了 Find X8 上的量产落地。在这个过程中,不仅要自己攻克技术问题,还要联动供应链厂商一起协同改进,刨去整条产线相关技术的研发与人力成本,单是厂房建设、产线设备和加工材料的成本,就超过了一亿元。正是这个工艺的改进,不仅带来了更完美的四边等宽极窄边屏幕,还提供了更好的防尘防水性能,并降低了日后维修的成本,品牌与用户共同受益。而这只是一个开始,OPPO 的工程师们早已开始投入新一代封装技术的研发和优化中。每一套模具都将从这个窗口走入产线,这里不仅是每一部 Find X8 屏幕封装的起点,也代表着 OPPO 自主研发能力的新起点作为普通消费者,我们更多听到的是各种潮流趋势和宣传引导,比如新时代的智能手机,AI 大模型碾压一切,软件和服务颠覆升级,硬件创新好像不那么重要了。作为科技内容从业者,我们也会经常执着于局部参数,习惯了对立争吵,忽略了用户的真实需求,以及对整个行业的共进思考。而每一次硬件体验的升级,都离不开供应链制造的不断精进,包括材料、工艺、制程、数智化的不断创新等。在这个过程中,供应商和制造商会交替迭代,也会共同成长,一起带来全行业的突破和进化,这正是中国制造的核心魅力。OPPO 正是一直坚持构建自主研发体系,沉淀深厚的工程化能力,给消费者带来更多优秀的硬件体验,同时也拥有更好的细节打磨和品控管理。我手中这块小小的屏幕背后,凝聚了无数中国工程师在背后的默默创新,也代表着整个中国制造的创新和未来通过本次探访,我深刻感受到,中国智能硬件行业的激烈竞争不仅要求人力的投入,更需要前沿技术的持续突破和工艺创新。OPPO在「四边等宽」屏幕技术上所做的技术投入和工艺优化,虽然仅仅只能算是行业迈向「中国创造」的一小步,但却代表了一个重要方向。这种以用户体验和技术积累为核心的创新路线,为中国制造业注入了新的活力。它不仅展示了中国制造的工程实力和创新能力,更是中国制造向更高价值链跃升的有力象征。随着技术和生产工艺的不断突破,我们有理由相信,「中国制造」终将实现向「中国创造」的全面转型,继续为全球用户带来更多创新的产品体验。未来,中国制造业将逐渐摆脱传统的成本导向型竞争策略,以更具技术含量的产品满足全球市场需求,进一步巩固在国际舞台上的地位。这种坚定的技术路线,也为全球市场带来更具价值的用户体验,驱动着整个行业的持续进步。